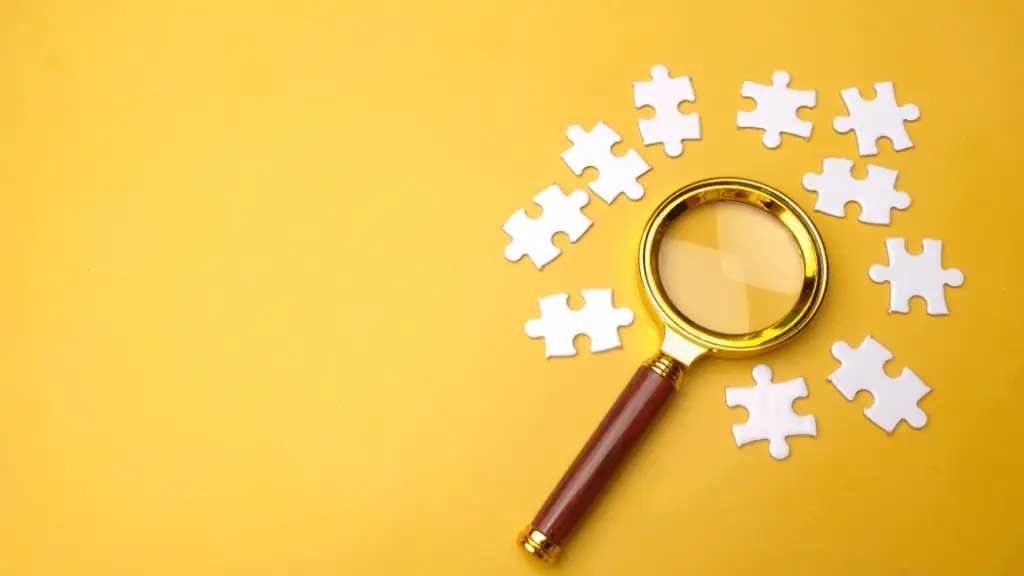
Mistakes happen, but learning from them
is critical. Investigating any slips in quality early can cut out performance issues down the line. By intervening early to get to the root cause of what went wrong, be it training, raw materials, or human/process error, you can understand how to refine your process and apply corrective actions.
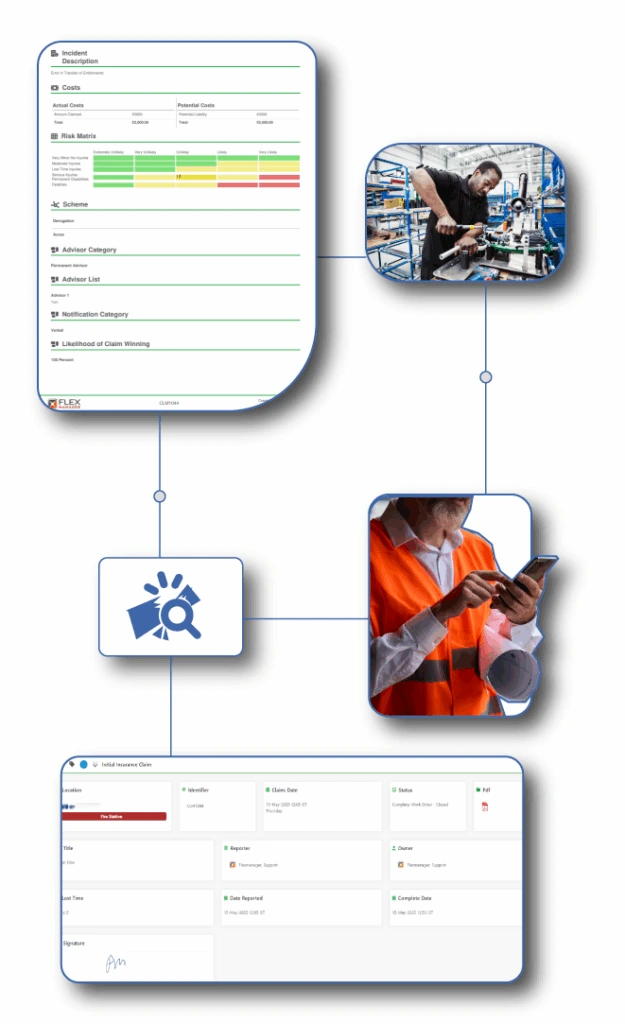
Defect Investigations
Key Features & Benefits
Clear review process
Ensure every defect is methodically reviewed in a process set by you, in a structured workflow.
Corrective actions
Assign and track resolution of investigations to prevent recurring issues, or further in the process.
Assess Level of Risk
Receive a report on how much of an impact a defect will have on the production process.
Mobile-to-desktop integration
Record defects on-site as they arise, escalating to desktop users as necessary, facilitating swift resolution.
What Can a Defect Investigations process do for You?
Thorough Root Cause Analysis
Investigate defects and quality issues thoroughly to identify root causes and implement effective preventive measures.
Effective Corrective Actions
Track and manage corrective actions efficiently to address identified defects and improve product or service quality.
Proactive Trend Analysis
Analyze defect data to identify trends and patterns, informing process improvements and preventive actions.
Customer Satisfaction
Improve customer satisfaction by reducing defects and enhancing overall product or service quality and reliability.
What we do
Connected Modules
Our connected module means you upload information one time and it will be recorded wherever relevant. Here are just some of the Modules connected to Defect Investigations.